“We know these chemicals are dangerous”
The realities of running an informal leather processing business inside Dhaka’s tannery industrial estate.
Introducing Nath and his business
Nath is the manager of a small and informal business unit within the BSCIC Tannery Industrial Estate in Hemayetpur in Dhaka. The estate is on 200 acres of agricultural land near the Dhaleshwari river. Bangladesh’s leather sector began relocating from Hazaribagh to Hemayetpur in 2014 to stop further pollution of the Buriganga river. Following some reluctance, factories were encouraged to make the 14km move in 2017 after the High Court ordered the gas, water and electricity connections to commercial units in Hazaribagh to be disconnected.
The business Nath manages buys raw cow and goat hides from different places in the country and then processes them for onward sale to four to five buyers serving the domestic leather market. Occasionally, he sells leather to traders or business owners inside the tannery complex, especially when he has high quality leather for the export market. He explained:
“We can get higher rates if we have good quality leather, and it is processed by skilled technicians. But if the leather is processed by unskilled workers, then the leather may become damaged”
Wet blue leather is tanned with chromium sulphate and chromium salts that gives it a light blue tint. It is also called chrome-tanned leather. Before reaching the wet blue stage, hides will have been put through seven other stages. Sometimes, Nath is contracted to do the entire process i.e., soaking, fleshing, unhairing, liming, deliming, bating, pickling and then the tanning of raw hides to turn them into wet blue leather. Sometimes the first seven processes are done by the client and Nath is only contracted to tan the hides with chromium sulphate.
The business premises is a one-story tanning facility, which consists of four tanning drums, a yard for cutting raw hides and mixing tanning chemicals and a roof which is used for drying the hides. The facility has a separate place for storing raw hides and a small tank for disposing of chemical wastewater.
It is typical for 12 people to work for this business each day, which includes four to five children. The children are engaged in drying leather, carrying salted raw hides from the local market (situated just outside the tannery complex), cutting leather and transporting processed hides.
Workers are hired without contracts and are paid according to what they produce. For example, children are paid according to the number of pieces of leather they dry and cut.
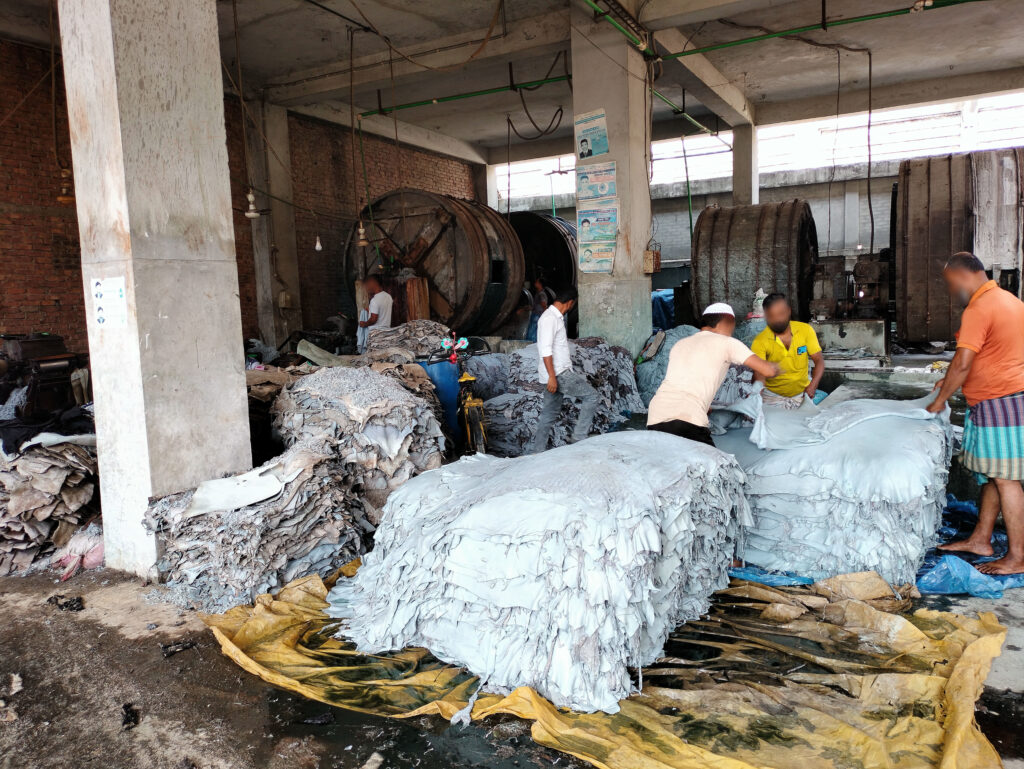
Piles of wet blue leather at Nath’s business unit
Work shadowing with Nath
In March 2022, two CLARISSA researchers accompanied Nath and his 12 workers for four consecutive days to observe in detail the day-to-day realities, practices and pressures of running an informal leather processing unit. The research team made in-depth observations of the multi-stage tanning process, learning from Nath and his workers about their roles and responsibilities. Sometimes the researchers would ask questions and have informal discussions to make sense of what they were observing. The team also spent time with children. At the end of each day the researchers recorded their observations.
During the shadowing process the research team observed the specific tasks and working environment of three children aged 15-17 years old. The research team also had the opportunity to learn the reasons why these children came to work in the leather sector in Dhaka.
The first meeting didn’t happen as planned because Nath was busy mixing chemicals to process 1,500 pieces of goat hide. The research team waited at a tea stall outside his facility until the evening. From a research perspective this delay was useful, as it identified how hands-on Nath was in the business operations and highlighted the socio-economic role of tea stalls in providing a place employees gather to socialise and learn about work opportunities.
The work environment and its dangers
Leather processing is a complicated multi-stage process, which requires many toxic chemicals.
Raw hides are inserted into a large drum for cleaning. Chemicals are added to water to wash the hides. Then chemicals are added to the drum again, this time for spinning and soaking for the liming and hair removal process. Then the hides are washed again, and another set of chemicals are added to remove the previous set of chemicals used in the liming process. Following this cleaning stage, acid is added before chrome and sodium are added to obtain wet blue leather, which is then sold for further processing. Wet blue leather needs to be shaved to obtain the perfect thickness and smoothness. At this enterprise workers shave leather using a shaving machine which needs fuel (diesel or kerosene oil) for spinning the motor belt.
As soon as the researchers entered the facility, they were struck by how unhealthy the environment seemed. It was very damp. The smell from the hides and the chemical processing was very strong. Chemicals were all over the floor, as waste products from the drums ran towards the narrow drains outside the factory.
During the four days of research, workers were observed mixing chemicals and undertaking the removal of blockages in waste fluids without any safety measures. All workers wore sandals, thus exposing their feet to chemicals. Nath showed the research team his hands and they looked wrinkled. He reflected:
When I mix the chemicals, my hands become wrinkled. I can’t move my fingers properly for a long time. When mixing chemicals, we must use hand gloves. but we do not use them always because, it is costly, and we face problems when mixing it with hides … We know these chemicals are dangerous. Even we use a chemical which is inflammable, within a second, it may be exploded, and I become seriously injured. There are several chemicals that are extremely dangerous, but we have to handle without safety measures …
The economics of leather processing
The profit margins for a small informal enterprise processing leather are small. If the business performs all the processing steps from raw hide to wet blue, the profit margin can be as low as 200 BDT (US $2) per hide.
These profit margins feel particularly small after observing the extent to which Nath has adapted his processing techniques to meet price points. He is conscious of the way he runs the business, suggesting we should go to a big tannery to understand “what a modern tannery factory is like”. Nath, like the modern tannery factories, strives to produce export quality leather but economics constrain the approach he takes to tanning leather, which in turn, negatively influences the quality of his products:
For making good quality products or export quality products we need an expert chemist. But we cannot bear the salary for an expert chemist. Their salary is beyond our capacity. As they have studied, they have more scientific knowledge on the perfect mixing of chemicals. If you employ a chemist, then there is less possibility of facing troubles about chemical use. We cannot mix chemicals as per requirement. For export quality leather, usually it requires 200 types of chemicals, but we use only around 20 types of chemicals. For this reason, rate of export quality product is higher than product for local market.
The more chemicals that are used, the better the quality of the leather. By contrast to the big tanneries, Nath manages without a chemist and with much fewer chemicals, increasing the risks that processing may go wrong. A single mistake can destroy thousands of pieces of raw hides. It’s also possible that hides will be rejected by buyers because they are not at the required quality and shipments are sometimes cancelled once processing has begun. In these scenarios the business makes a loss on a contract. There is no burden on the part of the buyer to meet processing costs and there is no business insurance to claim against. It is common knowledge that mistakes of this kind can result in a business closing.
Most of the time Nath buys chemicals from informal traders just outside the tannery complex, using a mix of cash and credit payments which he repays once he has sold the wet blue leather. If a contract results in a loss, there is no money to make these repayments.
For his workers, earnings are low, given the length of their days and the toxicity and dangers of their work environment. For example, the worker that operates a shaving machine receives 1.60 BDT (about US $0.01) per goat hide he shaves. One worker can shave between 400-700 pieces of goat leather in a day, earning them between US $6-11 a day. The pieces sell for between US $9-16. If the machine breaks down, the repair is covered by the owner of the business, but if the repair cost is below 200 BDT (less than US $2) the operator covers the costs to avoid any delay in what he can produce and therefore earn.
The children and their work
Three children, aged 15, 16 and 17 were working at the enterprise in March 2022.
During the work shadowing process CLARISSA researchers had the opportunity to learn why Aman and Raibal began working in the leather sector. Aman (15) carries raw hides and dries them while Raibul (16) cuts hides. Aman works because his family needs the income and Rabiul works to escape his education in a madrasa.
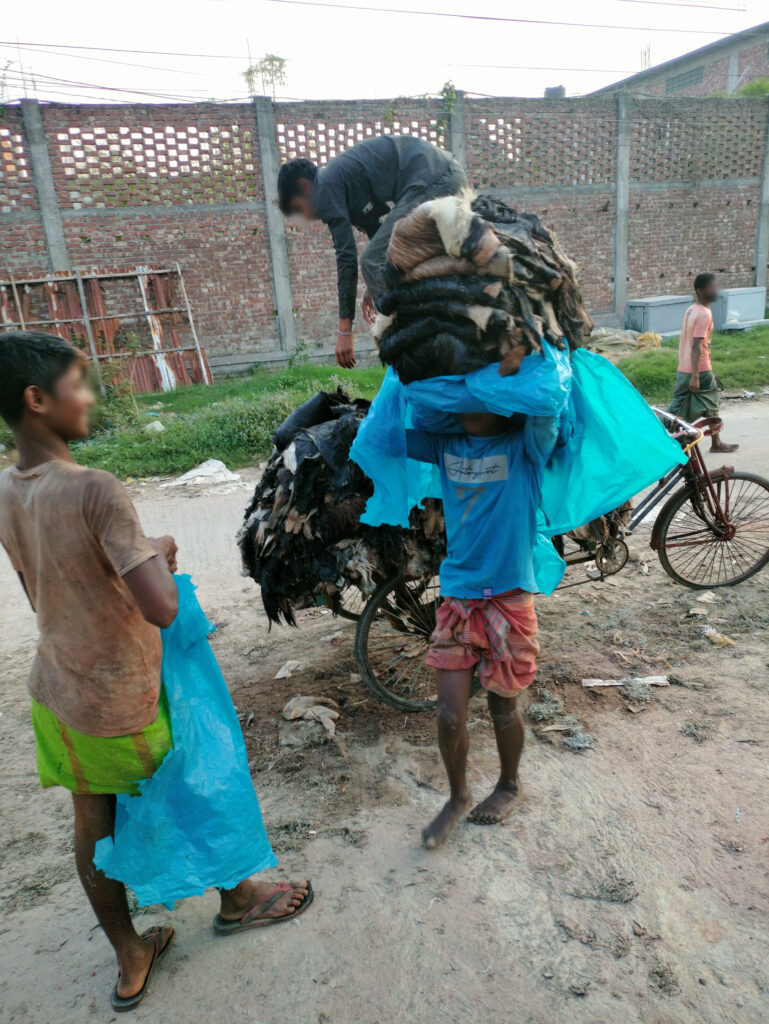
Children carrying raw goat hides.
Aman (15 years old)
Aman works in the business as a porter. He carries raw hides and materials from one location to another . He also dries goat leather on the roof of the premises. He also does same works in other factories. He came to Dhaka two months ago to increase what he can earn. He has two elder brothers who work but they are married and living separately now, so their income is not given to his family. When asked about his decision to work, Aman reflected:
“Boys of my ae or my friends are used to go to school. If I could do my study, I would be 9th or 10th grade student now. But this is my fate, if I don’t work, who will give food for me and my family?”
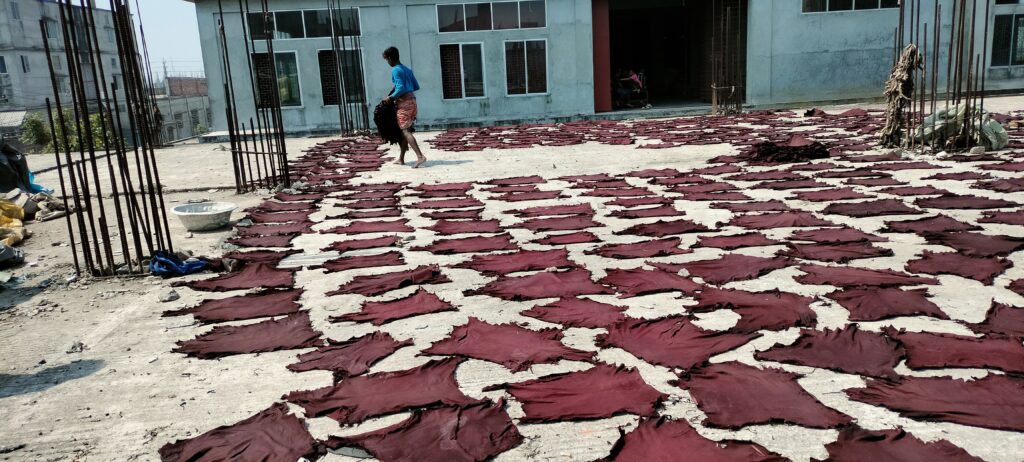
A child drying leather under the sun.
Rabiul (16 years old)
Rabiul cuts hides as part of a contract he was given to cut 2,000 pieces of goat leather. He looks very experienced with the knife. He works very fast to cut salted rawhides in the yard of the tannery premises. Rabiul shared his story about his engagement in the Hemayetpur leather complex:
“I used to study in a madrasa (religious school) in my village, but I didn’t like going. I wanted to study general education. But my parents insisted on a madrasa education. My father told me ‘If you don’t want to go to the madrasa you don’t need to study any more’. As I had no interest to study in a madrasa, I became inattentive, and the teachers punished me. Then I fled from the madrassa and started work. My uncle brought me here to work. He got a percentage for me. I got BDT 0.60 (US $0.0055) per leather hide I cut, and he took BDT 0.20 (US $0.0018.”
When children do the same work as the adults, they tend to produce less, which means overall they earn less. For example, the children can cut 700-800 goat hides in a day compared with the adults who can cut 1,200-1,400 hides in a day. At BDT 0.6 per goat hide, the children earn between US $4-4.5 a day compared with adult earnings of US $7-8 a day. Typically children work from 8am to 8pm in the evening. But when there is an emergency shipment the children work for longer, which explains the variability in their productivity and earnings.
In the case of Rabiul, his uncle found him work, and in exchange the uncle takes a commission on the money Rabiul earns.
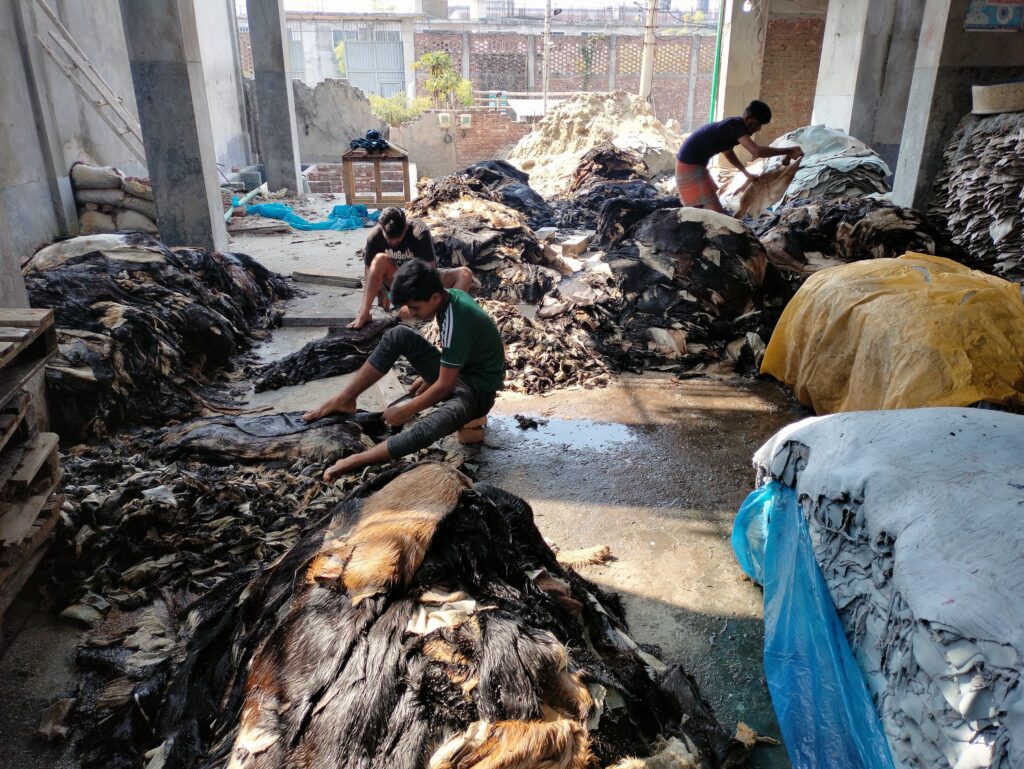
Rabiul sitting on the floor cutting goat hides with a knife.
Tea stalls
There is a tea stall in front of Nath’s tannery, where tannery workers and sub-contractors gather at break times and after work. This tea stall is a communication hub, where workers share information and search for jobs. One person said,
“I am waiting here to get a job”.
Another person said,
“we have heavy workload in our factory, you can work here”.
In another conversation two workers were eager to take the same contract.
The main gathering happens in the evening time, when the tea stalls become an outdoor recreational centre. People watch movies, play carom, cards or ludo. During one break someone was gambling on cricket. Everyone was interested about what he was doing and whether he was losing or not. Another person warned him about the bad consequences of gambling, and he replied,
“Life is short, enjoy it brother!”
Conclusion
Work shadowing with Nath in the Hemayetpur tannery complex was a valuable opportunity to observe the day-to-day work of children engaged in the leather tanning process for domestic and export markets.
This work shadowing exercise generated evidence on how children carry raw hides from the nearby market to the factory premises, as well as being engaged in drying leather, carrying chemicals and spraying leather products. The children were either paid by task or by what they produced, earning less than adults for the 12 hours they typically work each day. Even though these tasks should be carried out by adult workers to comply with labour standards, some factories prefer to engage children at a cheap rate. This is because in businesses like Nath’s, the children’s involvement is integral to business operations.
Despite working without a trained chemist on site and adapting his processes to greatly reduce the number of chemicals he uses, Nath’s profit margins are very low. Adapting processes in such a way introduces precarity into the business model. For example, it means he can achieve lower quality leather and lower price points in the domestic vs export market. There is a risk of losing product if the processing goes wrong. Nath also incurs losses when orders get cancelled once processing has begun. Without any safety net or business insurance for when things go wrong, a cheap and flexible workforce is important for Nath to offset the risks and pressures he faces. He is stuck in this operating cycle because he cannot generate sufficient profit to reinvest into his processes to sell higher quality leather at higher price points.
The work environment in Nath’s tannery is not a safe environment for his workers. Chemicals that are acknowledged to cause a range of health problems, including skin irritations, respiratory issues and cancers are everywhere and no safety equipment is used. The physical effects of these chemicals are apparent on the owner’s hands.