Working with poor infrastructure in poor health
The realities of running a tannery inside Dhaka’s Tannery industrial Estate, Bangladesh
Introducing Jahangir and his leather tannery
Jahangir is the owner of a small tannery within the BSCIC Tannery Industrial Estate in Hemayetpur in Dhaka. Jahangir inherited the business from his father who began operations in Hazaribagh in the 1980s.
Today, 38 years later, the premises for the business Jahangir inherited is a one and a half storey building. Leather processing activities related to tanning – soaking, fleshing, dehairing, liming, deliming, bating, pickling – happen on the ground floor. There are two shaving machines and three tanning drums for chemically processing the leather, but only two are functional. On the roof of the ground floor Jahangir has constructed a room to do paperwork and meet clients and subcontractors. The remainder of the roof is open to the sun for leather drying. He rents some land for dyeing work.
The business carries out the ‘wet blue’ process, using chromium sulphate and chromium salts to treat hides before they are dried, dyed and finished. Between 12-36 continuous hours are required to complete a wet blue process, depending on the composition of the animal hide and the quality required. The wet blue process is a critical stage in the leather making process because the precision of the treatment determines the softness, pliability, and durability of the product.
If Jahangir is given a contract to produce finished leather, he does the wet blue processing and then sub-contracts another business to produce finished leather. After receiving finished leather from sub-contractors, he dyes it according to his client’s preference. He then makes the final delivery to the client. He does not serve the export market directly, because his business does not meet the standards to do so, but he does serve the export-oriented factories through sub-contracts. This happens when formal factories receive contracts from foreign buyers and then commission smaller enterprises to product export-quality leather.
The business has ten workers, including Jahangir who himself works with leather. The workforce includes two children. A 16-year-old child is a staff member of the factory, and a 13-year-old child accompanies his father to work to help him earn money. All workers are hired without contracts and earn according to what they produce and sell.
Jahangir is well respected, as an employer and as a businessman. His factory is frequently open 24 hours to deliver orders on time and his employees help bring work to the factory, without commission. One employee explains:
“Because of his hard working and risk-taking qualities, Jahangir bhai (brother) could establish his own tannery.”
Work shadowing with Jahangir
In March 2023, CLARISSA researchers accompanied Jahangir and nine workers for four consecutive days to observe in detail the work environment, the multi-dimensional activities of the business and the practices of the owner and the workers. The researchers observed how the business and Jahangir interacts with clients, sub-contractors and workers, and they learned about business finances. At the end of each day the researchers recorded their observations and the details of their conversations.
During the shadowing process, the research team observed three types of work carried out in the factory premises (tanning, drying, and shaving) as well as the dyeing and spraying of leather which happens nearby at a place that Jahangir has rented. The researchers accompanied two men whose responsibility it is to operate the tanning drums, two men who shave the leather, one man who dyes the leather, one man who sprays the leather and two children aged 16 and 13 years old who dry and sell leather. The research team also had the opportunity to speak with clients and sub-contractors of Jahangir, learning about the business-to-business relationships that underpin the contracts the tannery receives. Here is a short profile of the employees the CLARISSA team got to know:
Drum operators:
- Atahar, in his 40s has a wife and three daughters. They live nearby. He earns BDT 19,800 (US $180) a month.
- Rustam, the older brother of Jahangir, lives in the residential area of the tannery complex with his two daughters. He earns BDT 29,700 – 39,600 (US $270-360) a month.
Leather shavers:
- Razzak, in his 50s lives with his wife and three daughters. His earnings vary according to the seasons, between BDT 14,300-19,800 (US $130-180) a month.
- Kamran in his 20s lives with his wife, daughter and two sons. He also earns between BDT 14,300-19,800 (US $130-180) a month.
Leather dryer:
- Shajib, 16 years old, is new to the work and to the city. His family live in the city, and he lives in a boarding house.
Leather sellers:
- Malik Mia lives with four family members nearby. He collects processed leather for selling, earning BDT 22,000 – 24,700 (US $200-225) a month.
- Raja, 13 years old, is the son of Malik Mia. He works to increase his father’s productivity to pay off loans taken out to pay for his mother’s health treatment.
What happened at the tannery
Day 1
When the CLARISSA researchers arrived at the factory at 11:00 am, Atahar and Rustam were bringing out wet blue leather from the spined tanning drum. Both the workers were wearing lungies (traditional garment worn instead of pants). None of them wore gloves, boots, goggles, masks, or any other safety equipment.
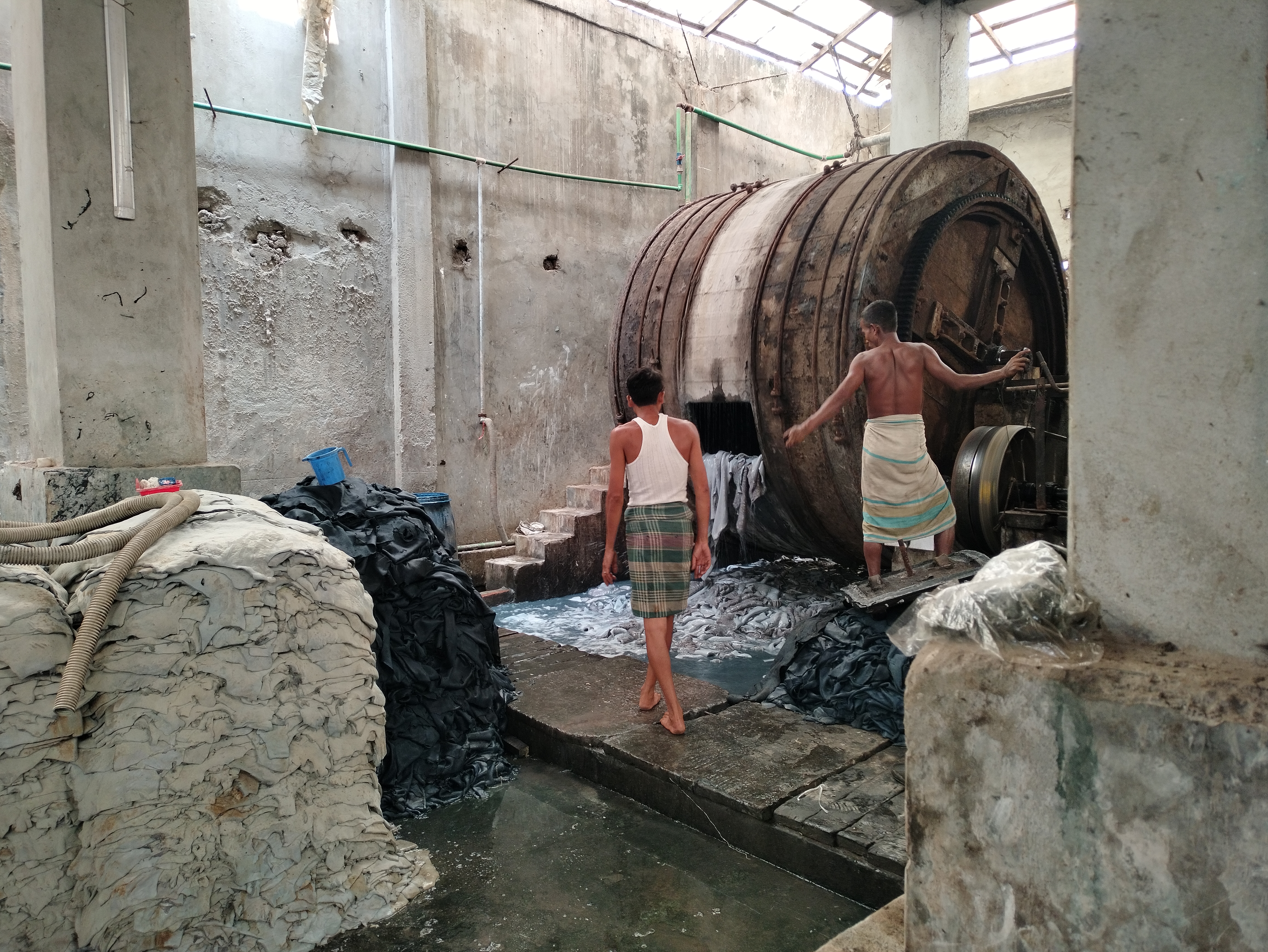
Razzak and Kamran were shaving dried wet blue leather using shaving machines situated on opposite sides of the entrance to the tannery. Beside each machine, two piles separated the shaved from the unshaved wet blue leather. Besides those, there were piles of shaving dusts.
Jahangir was in his neat and clean office where he holds meetings with buyers and contractors. On the ground floor, the drum and shaving machines create an unbearable noise. If anyone wants to talk, they must shout.
Around 12:30 pm the electricity went out. The machines stopped suddenly and there was silence. Jahangir provided a tour of the factory and introduced everyone. Workers were cordial and cheerful. It was observed that even when working, colleagues were making fun of each other and laughing.
While the electricity was out, everyone went home to have lunch. Jahangir said he and his brother prefer to eat lunch and rest at their houses, which are nearby but that when the work pressure is high, they eat in a restaurant just outside the tannery complex.
By 1:45 pm the electricity was still out. Suddenly it started raining. The leather was getting wet, but Razzak observed that this is good, as the next step is to soak the leather in water for re-chroming.
The electricity came back on between at 2pm but went out again one hour later. One of the drum operators became agitated because the leather was in the drum and this process requires a continuous electricity supply (or the leather and its quality becomes compromised).
In the evening two of the men shaving leather stopped their work at 8:00 pm and left the factory. Jahangir left the factory at around 9:00 p.m. One drum operator stayed at the factory until 12:00 am to continue the tanning process that was disrupted from the electricity outages.
Day 2
A researcher arrived at 9am as this was when the factory was supposed to open, but he found Razzak and Kamran already there, shaving wet blue leather. They explained that they had started work at 7am to try and compensate for the electricity outages the day before. In the early morning there is more likelihood of getting an uninterrupted electricity supply. At 9:00 am Atahar, Rustam and Jahangir arrived. By 9:00 am the electricity had stopped, and the workers spent their time taking out wet blue leather from the drum.
At 10:00 am a buyer came to the factory. Jahangir apologised to the buyer for not finding the time to visit him at his office. He explained that the electricity supply interruptions had affected productivity, even though they still must deliver products on time. The electricity came back on, and they could not continue the conversation, so they went to Jahangir’s office.
The other workers put another set of cow head hides into the drum and poured in chemicals. They started the drums, explaining that they need 15-16 hours to complete the tanning process for these hides today.
Jahangir took his buyer to a nearby tea stall. The researcher went to the roof of the tannery where he found Shajib drying leather.
At around 5:00 pm Kamran left the tannery for home. Razzak stayed to do more shaving. Atahar organised the leather in the factory. At 6:00 pm Jahangir left to deal with a family matter in Hazaribagh. Rustam went out but came back in the evening.
The tannery ran until 3am in the morning. Atahar stayed in the office room so he could turn the drum off at the correct time.
Day 3
Jahangir arrived first at 9:00 am and started cleaning the tannery. One by one everyone entered and began work. Kamran did some maintenance of the shaving machine. He examined different parts of the machine, cleaned them with cloth, and then poured some lubricant oil over them. With the help of Jahangir, Atahar started taking out the processed wet blue leather from the drum.
At 10:00 am, Rustam took off the main gate to the tannery and started repairing it. The last two times they hired a professional to do this, but as Rustam has observed the process carefully he is able to fix it on his own now.
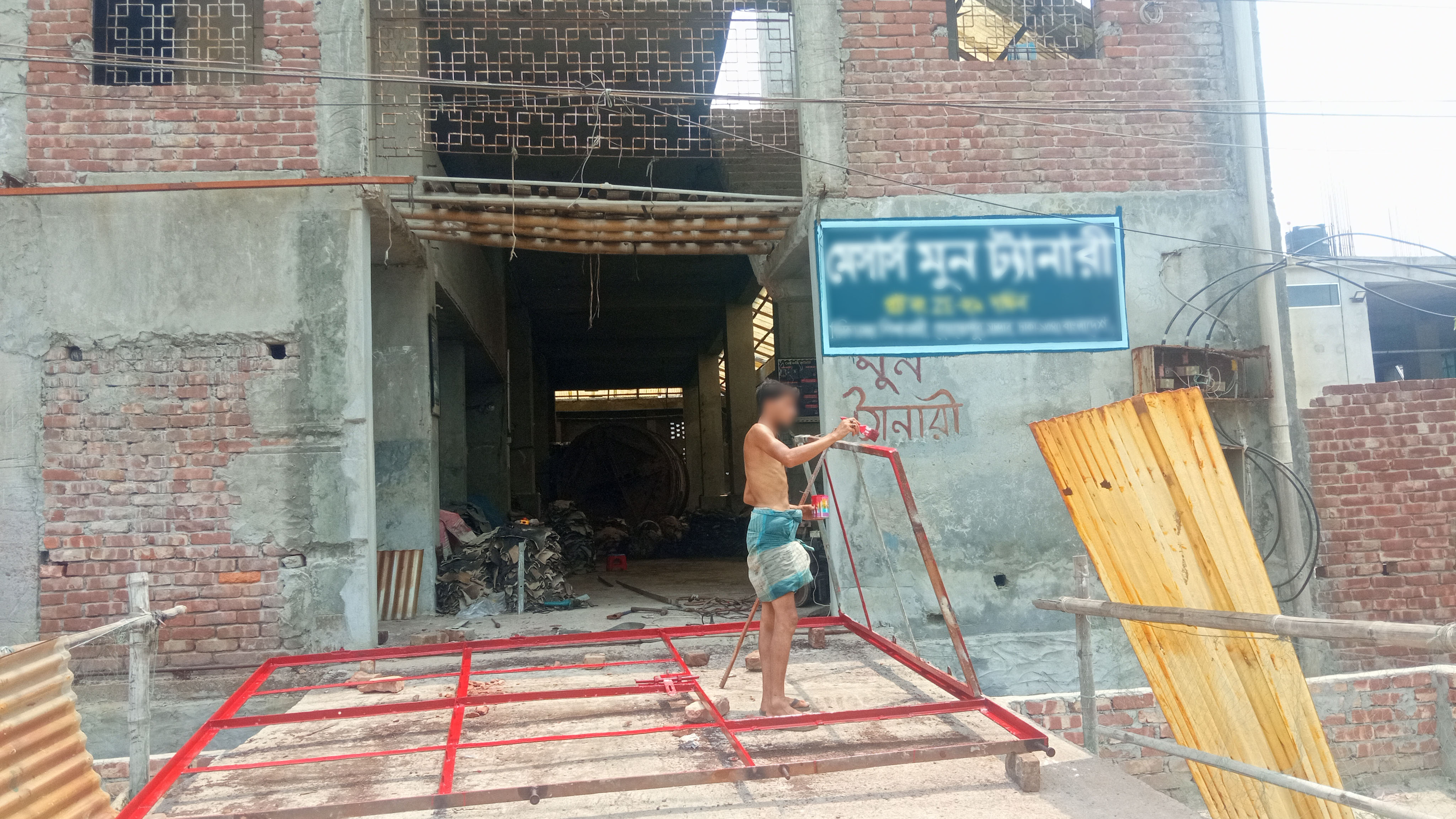
After lunch the electricity went out again. Shajib and Rustam left the factory in the afternoon. Kamran and Razzak continued their shaving activities until 8:00 p.m. and then all the staff members left the factory. Before leaving the factory, Jahangir put some leather into the drum and turned that on. The electricity supply is more consistent at night so he was hopeful that the process would run more smoothly.
Day 4
Jahangir reached the factory first. He climbed up and opened the drum and reached inside to take out a sample. He concluded that the leather would be ready to come out of the drum by the afternoon.
At around 9:30 am Jahangir left the tannery to go to the Bangshal area to collect dues from a client. Jahangir considers the client to be a good buyer who always pays on time. He planned to collect BDT 150,000 (US $1,360) and then go directly to Hazaribagh to deposit the money in the bank. Before leaving the tannery, he called his brother, Rustam, over the phone and informed him about the ongoing tanning process. He asked his brother to take out all the processed leather from the drum with the help of Atahar after the completion of the tanning process.
At 10:00 am the electricity went out. Everyone stopped their work. Most of the workers left the factory. Razzak passed the time sitting on his chair. After an hour the electricity came back on, and everyone resumed their work.
At 12:15 pm a sub-contractor arrived with a rickshaw van carrying sacks of chemicals. As he wasn’t able to use the factory premises of the factory that sub-contracted him, he had come to use Jahangir’s tannery. He delivers the hides and the chemicals to the tannery and Jahangir’s staff process the leather and provide him with wet blue leather. The subcontractor then delivers the wet blue leather to his client, who delivers the final products to the end client. The sub-contractor’s client gets the full payment amount. The sub-contractor gets a lesser amount and Jahangir receives less again. The sub-contractor explained “This is how we run our business. From one order different people make their own profits”.
Workplace toxicity and the effects on worker health
There are notices hung on the walls in the tannery, with warnings such as: “Persons under 18 years of age are not allowed to work in this factory premises.” and “Danger: Drum area; This area is contaminated with harmful chemicals. Failure to use protective equipment may cause serious health issues”.
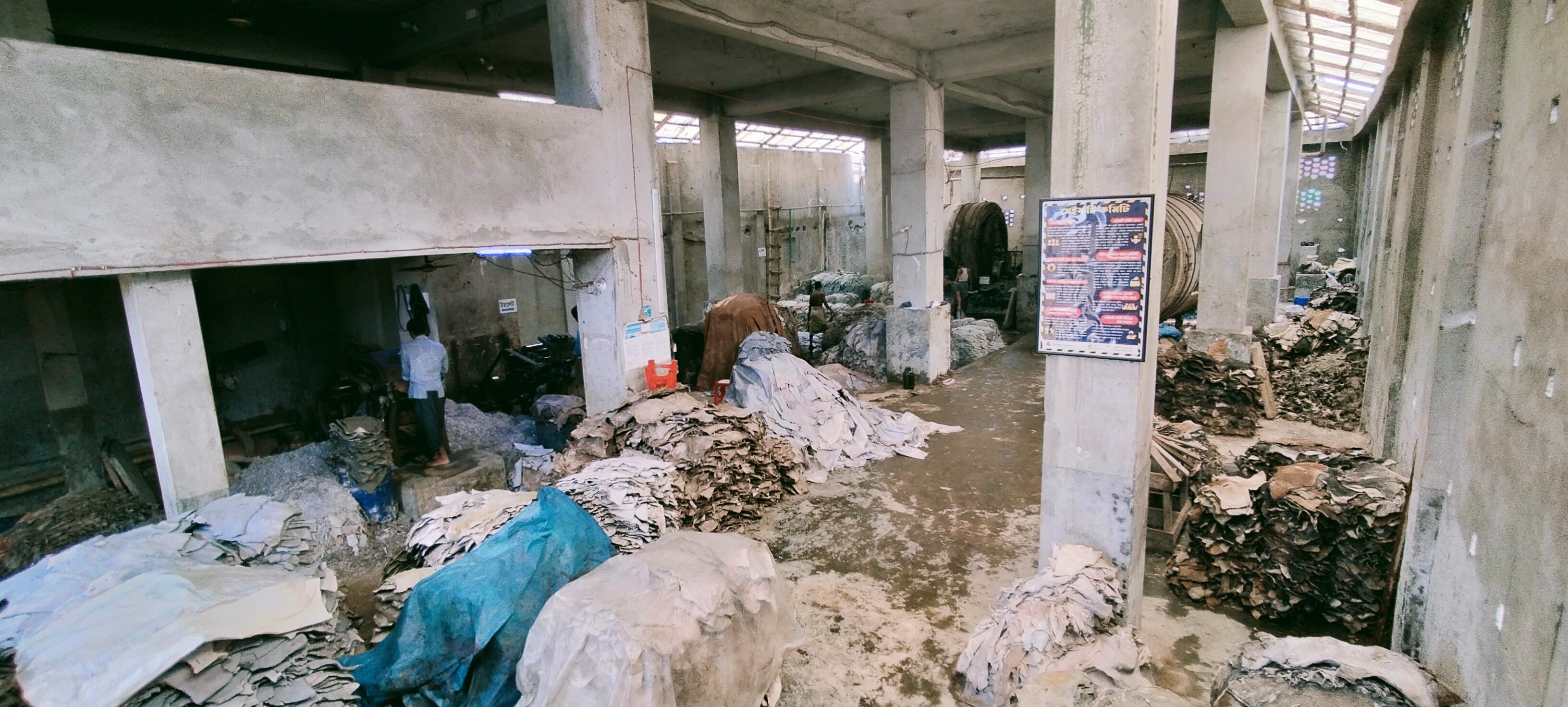
Practice however is not in line with the notices. Workers at the tannery work without any occupational safety equipment and two children work at the tannery.
A conversation with the drum operators revealed the health implications of their work:
Rustam: “This job is not good for health. While working, we deal with almost 200 harmful chemicals including chromium, sodium, sulphuric acid, hydrogen sulphide, etc”.
Atahar: “If someone deals with these chemicals for a long time, he suffers from different severe diseases”.
When Jahangir was asked why the safety rules on the signs are not followed, he replied “How can we follow them? We’ll lose all our money buying occupational safety equipment.” He explained that the workers in tanneries suffer from respiratory diseases, skin diseases, serious headaches and many other health issues. Razzak, who shaves the leather, used to work with chemicals but “then some health issues emerged”. He suffered a skin disease for several years which he described as “horrible”. He explained:
“I was an expert in tanning. I was very skilled in mixing chemicals. That’s why some factories hired me as a consultant. I used to give instructions to the workers, and they used to mix them. But once the worker became an expert the companies used to fire me and hire that worker in a permanent position. I lost three jobs that way. So I started doing other works”.
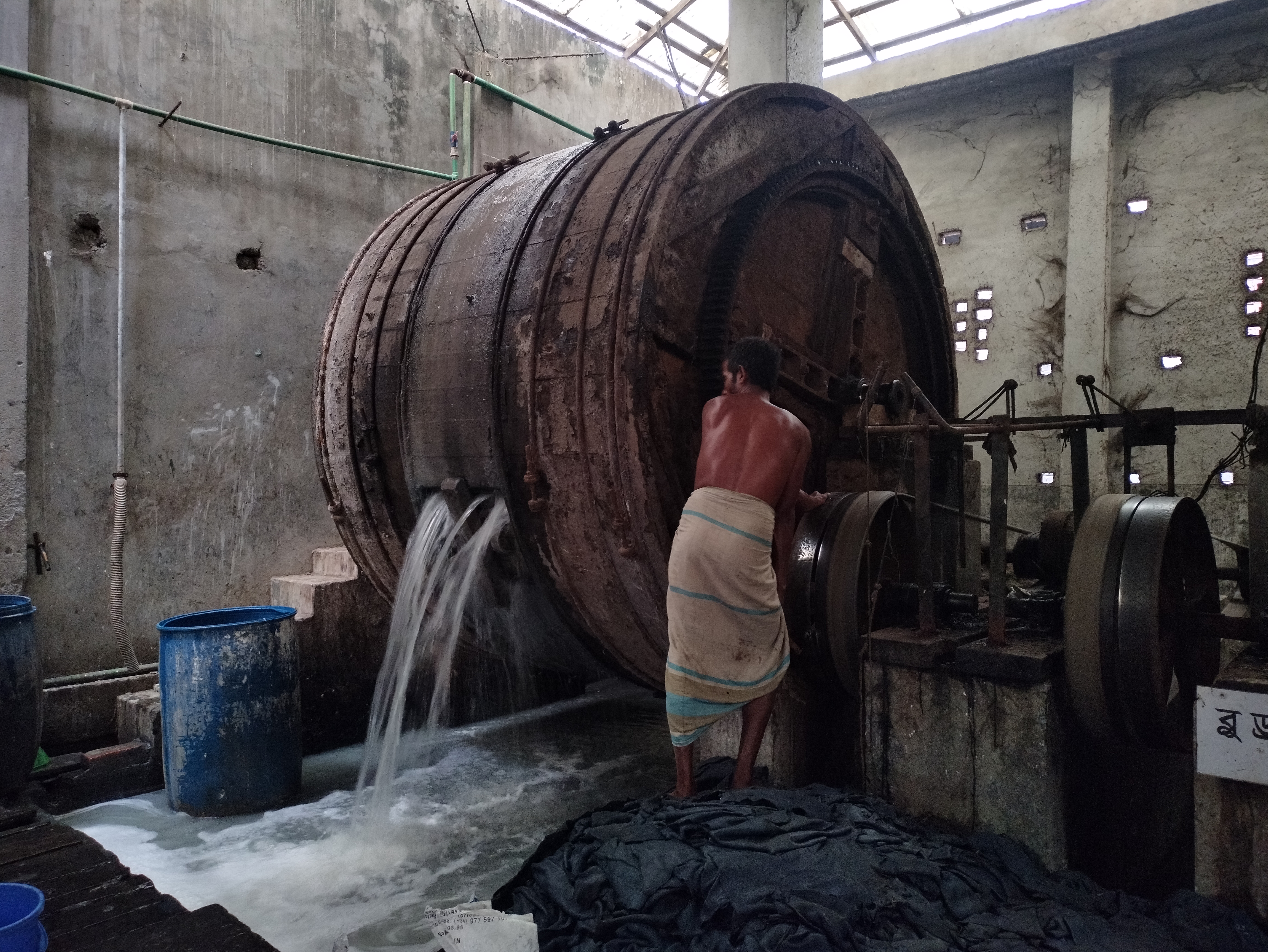
Jahangir described a health situation that is worsening, which is resulting in in the treatment costs for workers in Hemayetpur increasing. He says that this is because people are eating vegetables grown in soil that has been polluted by hazardous chemicals, including chromium, in wastewater. When they worked out of Hazaribagh they got fresh vegetables from different parts of Bangladesh. Here, the locally grown vegetables are cheaper, so most workers purchase them at the local market and eat them.
It is widely known by governments and the leather industry that chromium used in the wet blue process is particularly harmful to human health, causing skin irritation, asthma and cancer. Leather shavings have high levels of chromium and the dust that occurs from leather shaving is carcinogenic. Neither of the workers responsible for shaving in this tannery wear masks. There are three fans on the premises and two are in the leather shaving area. More chemicals linked to respiratory diseases are used in the dyeing and spraying of chemicals. This work takes place outside, but the workers do not use masks.
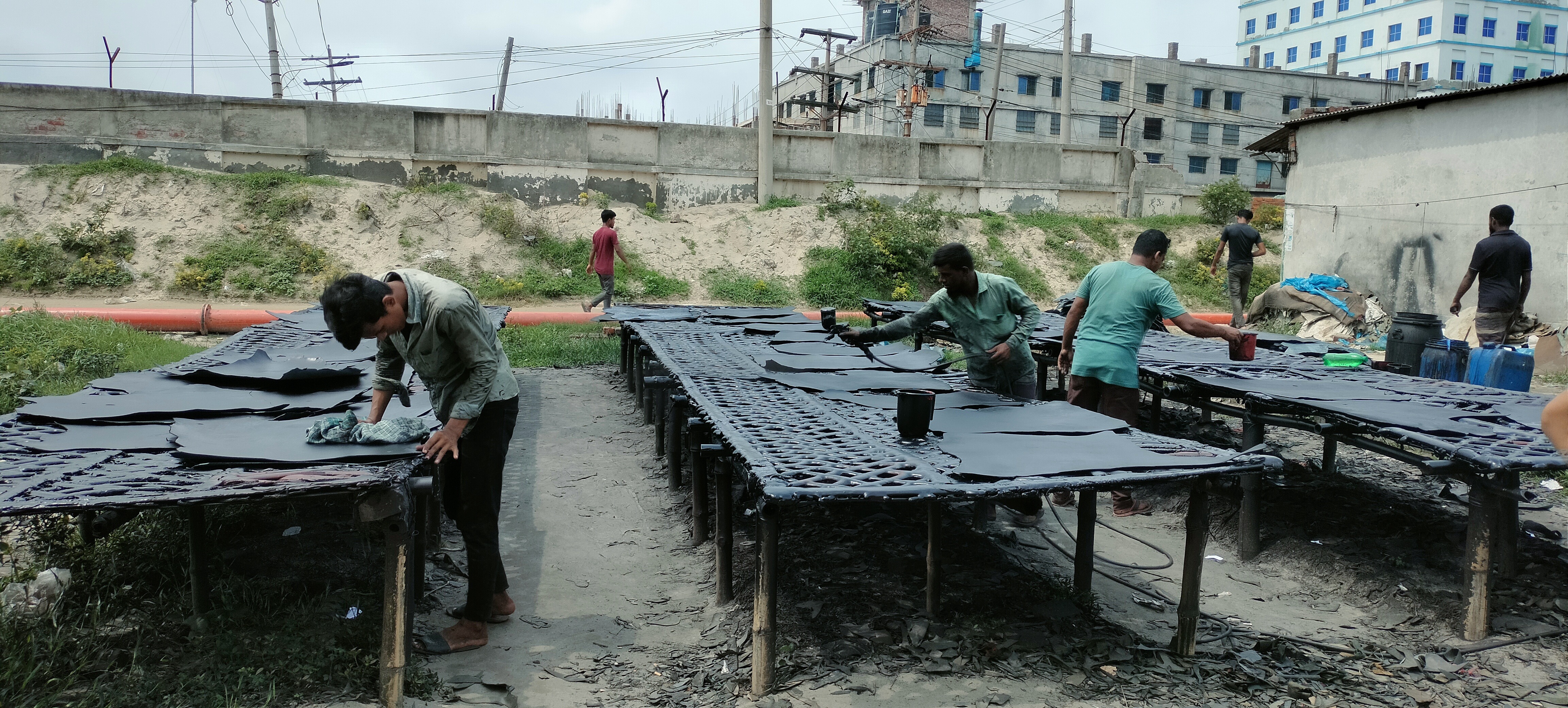
The workplace is incredibly loud when the drums and shaving machines are in operation. Unaccustomed to the noise levels, the CLARISSA research team found the noise almost unbearable. No safety devices are worn by any staff to protect their hearing.
The children working at the tannery
Shajib, 16-years-old, works under the direct sun for a long time. His work begins when the sun rises. When the sun goes down, he organises all the dried pieces of leather. He works on the roof by himself, and he stays there most of the day, without interacting with the adult workers.
Shajib started working at the tannery two months ago, after he decided to quit school (which was a result by him being beaten and scolded by teachers). After he left school, he spent his time with friends on the streets, but his parents were not happy with this so sent him to the tannery to work. (At first, he had tried to find a job in his village, but he couldn’t find anything regular and then someone he knew in the village told him about the job in the tannery). He now lives in a “mess” (a type of accommodation) with the person who brokered the job for him. All the boarders share the costs of their food and someone to cook for them. Shajib earned BDT 7,000 (US $63) the first month he worked at the tannery. He explains:
“Now I earn very little money. I need to spend all my money making my own living. When I’ll be able to earn more, then I’ll save some money and send some money for my parents and sister in the village.”
He hopes to gain more experience:
“The workers who have good connections can get regular work and earn BDT 20,000 – 25,000 (US $181-227) a month. Gradually when you become a sub-contractor you earn more. Right now I am working under a sub-contractor. I am not skilled yet to do technical work. That’s why I only dry leather. When I become experienced, I’ll be able to do other jobs like tanning, shaving and dyeing. Then I’ll have connections with lots of people and I’ll be able to earn more”.
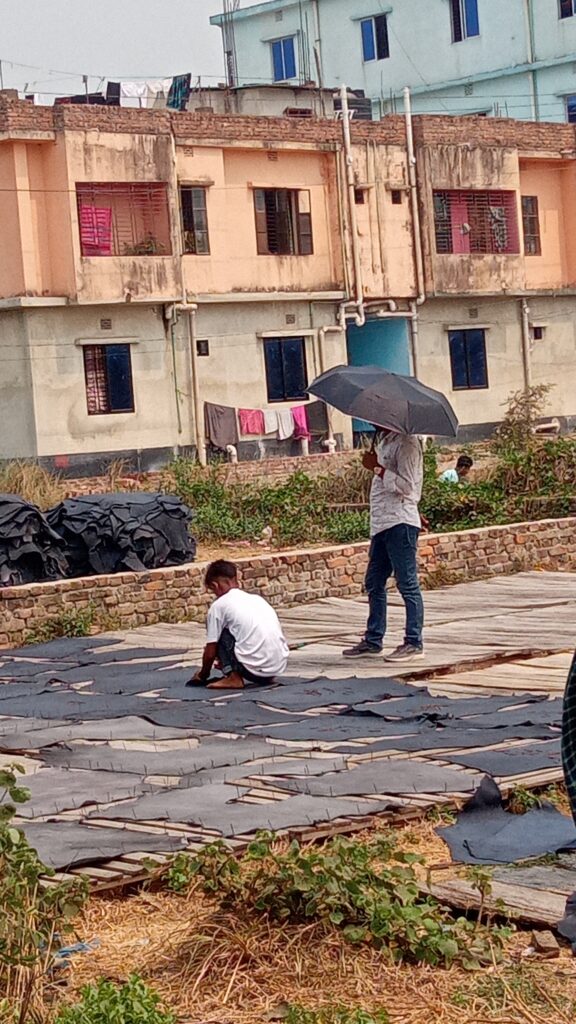
A child drying leather under the sun.
Raja is 13 years old and accompanies his father to work to collect processed leather for sale. He also dries leather outside in the sun, but he does not do technical jobs like tanning or shaving. Raja and his father live near the tannery complex. Raja enjoyed school and passed class four in 4th place among 80 students. He also passed class five with a good result but when he was in class six, his mother became sick, and his father took out a large loan to pay for her treatment. Raja then started working alongside his father to clear the debt. Together they can earn BDT 22,000-25,000 (US $200-227) a month. Raja is upset that he can no longer attend school. After a long day at work he does not feel well enough to study. His father explains:
“I understand the importance of education very well. But we do not have any other way. My son was doing very well in his school, but I am not able to send him to school now. Maybe, when all the debts will be clear, again, I’ll send him to school unless I have to take a loan again. Because anytime any crisis may happen. We cannot predict anything.”
The economics of the tannery business
Jahangir earns money through the business in three main ways:
- He or his staff win business from local buyers and Jahangir receives direct payment.
- Sub-contractors of larger factories, often serving export markets, contract the tannery and its staff to conduct the wet blue part of leather processing. Jahangir receives a percentage of the full payment.
- Independent business owners collect wet blue or shaved leather and sell to local product manufacturers. Jahangir receives a percentage of the sale.
Profits are at their highest when one of the big factories gets a large international order and Jahangir is subcontracted – this earns a good profit. Large factories are however currently getting fewer contracts from international clients. For his own sustainability, Jahangir takes orders from clients serving domestic markets, although this work is lower paid, partially because the leather used is lower quality.
To run the business Jahangir has fixed costs of more than BDT 100,000 (US $900) a month, which include:
- Electricity – BDT 35,000 (US $320)
- Water – BDT 35,000 (US $320)
- Loan repayments – BDT 30,000 (US $270)
- Land rent – BDT 1,666 (US $15)
Jahangir also spends approximately BDT 100,000 (US $900) a month on production-based wages. The child worker receives the lowest wage of BDT 7,000-9,000 ($60-80) per month and the owner’s elder brother, who is a skilled ‘drum man’ earns the highest wage of up to BDT 40,000 (US $360) a month.
In addition, Jahangir spends money on raw materials, including raw hides, and the many (200) different chemicals that are used in the wet blue process.
After incurring all these costs, Jahangir can make a profit of BDT 40,000-50,000 (US $362-453) per month. Although Jahangir is making a profit, he is not satisfied as he is not earning enough money to repay his partner’s investment and to reclaim full ownership of the business. He is also keenly aware of the precarious nature of his business. Sometimes he makes a good profit but at other times, for example when his clients cannot pay him, his capital gets stuck. As a result he does not take loans from banks as he would be at risk of defaulting on the loan instalments. A lack of capital is a serious concern for Jahangir. It renders him vulnerable when providing products on credit and it prevents him from hiring an experienced chemist:
“We need to hire a professional chemist. But in the entire month, I cannot earn the equal amount of a professional chemist’s salary”.
Jahangir runs his business without any written agreements, a strategy he employs to save money. He takes on work according to promises that clients make. He feels it would be difficult for people to “cheat” him because he knows the business so well, but the absence of written agreements does of course expose him to some risk. He explains:
“We run our local business based on clients’ promises. We even run the export-oriented business based on clients’ promises. Because we are sub-contractors … The big companies use stamp papers to do an agreement, but we do not have that kind of skilled manpower to deal with those types of business documents. To manage those types of activities we would have to hire a skilled manager.”
Impact of the relocation from Hazaribagh to Hemayetpur
Bangladesh’s leather sector began relocating from Hazaribagh to Hemayetpur in 2014 to stop the pollution of the Buriganga river. Following some reluctance, factories were encouraged to make the 14km move in 2017 after the High Court ordered the gas, water, and electricity connections to commercial units in Hazaribagh to be disconnected.
In 2017 Jahangir was allotted a 400 square metre plot to re-establish his tannery on 200 acres of agricultural land in Savar’s Hemayetpur near the Dhaleshwari river. To relocate and reorganise his tannery Jahangir took out a loan of BDT 10,000,000 ($90,000) from an acquaintance in return for a 25% share in the business. Six years later Jahangir continues to pay his business partner as part of their profit-sharing agreement.
The economics of the leather supply chain
Although there are many businesses, sub-contractors and workers making a living from the leather supply chain, the margins are small. Leather shaver, Razzak, explains:
“I get payment at a piece rate. For the shaving of one big cow’s hide, if Jahangir gets BDT 12 (US $0.10), I will get BDT 4.50 ($0.04) as my wage.”
Business-to-business transactions are structured by credit arrangements. Challenges arise with this system when someone defaults on a payment, as this affects other businesses in the supply chain. When Jahangir was asked about a client that he took to the tea stall, he said:
“He is one of my old clients. Two years ago, I received an order from him. He was supposed to pay me BDT 200,000 (US $1,800) but due to lockdown because of COVID-19, he suffered a huge loss. He paid me BDT 100,000 (US $900) and stopped all communication. A few days ago, he started communicating with me again. He told me that during that time he could not sell all his products; that’s why he could not clear my payments”.
Jahangir went on to explain that his client is a good person who had a good transaction history, which is why he took the risk to deliver that a huge amount of products on credit. But when the client couldn’t sell his products it impacted Jahangir, in terms of profit, and put him in a position where he could not reinvest capital as he needed to.
In a different conversation Razzak, who started working in the leather sector in the 1980’s reflected that clients used to pay their bills immediately after receiving an order, but that now, because the sector is not flourishing, everyone is running their businesses on credit. Razzak suggests that the decline in the sector’s profitability is attributable to powerful businesses controlling the sector, including syndicates who have the power to make the price of raw materials go up or down.
Jahangir feels the impact of what he considers to be unfair trading practices. Larger factories receive tax exemptions from importing chemicals from overseas and form into syndicates that artificially raise the price of chemicals. As a small business he cannot raise his voice against these syndicates and cannot negotiate better prices. This perspective was shared by a sub-contractor who told the CLARISSA team:
“Now, it has become very difficult to run the business. Mainly, the chemical sellers and the big business owners are making unusually big profits. Some leading chemical sellers created a syndicate to monopolise and to increase the price of chemicals in the market. Mainly, the chemical business syndicate made this chemical business sector highly monopolized and profitable. Because of paying high price for chemicals the leader producers cannot make a good profit margin … Previously, this sector was not like this. People used to have humanity. But now, everyone just wants to make their own profit by doing anything. No one cares for others”.
When probed about why this is happening, the sub-contractor stated that people from outside the sector influence how the supply chain works:
“They have capital, and they invest money to make a good profit. They do not feel for other business owners of this sector. We used to have a brotherly feeling with other business. owners. But now, the outsiders consider everyone as their rivals. The big shots always exert their power.”
Such discussions reveal the power dynamics that structure the economics of the leather supply chain. As small factories are unable to receive orders directly from foreign buyers, formal factories hold all the power. At the same time, formal factories cannot deliver orders without the smaller, informal factories. They depend on one another, even though unfair trading practices suggest that there is an asymmetric trading relationship between the two types of business.
Poor infrastructure
A lot of the challenges that Jahangir faces are linked to poor infrastructure in the Hemayetpur tannery complex.
Electricity supply failure is evidenced to be an everyday problem, affecting productivity, and lengthening the workday, sometimes extending it into the early hours of the morning. Intermittent electricity is particularly challenging for the tanning process, which requires a consistent supply to preserve the quality of the leather. Workers refer to electricity outages as “load shedding” suggesting that they are scheduled by the government to manage usage.
A lack of waste-water treatment facilities is also a persistent issue. Jahangir feels that the Central Effluent Treatment Plant (CETP) is not working properly. In his view government officials should have taken recommendations from the Institute of Leather Technology about the required capacity of the CETP. As a result (of not doing so), the treatment plant cannot process all the pollution that is released every day. Almost 200 harmful chemicals are used for tanning processes. Drum areas are barricaded so that factory areas do not get flooded with chemical water.
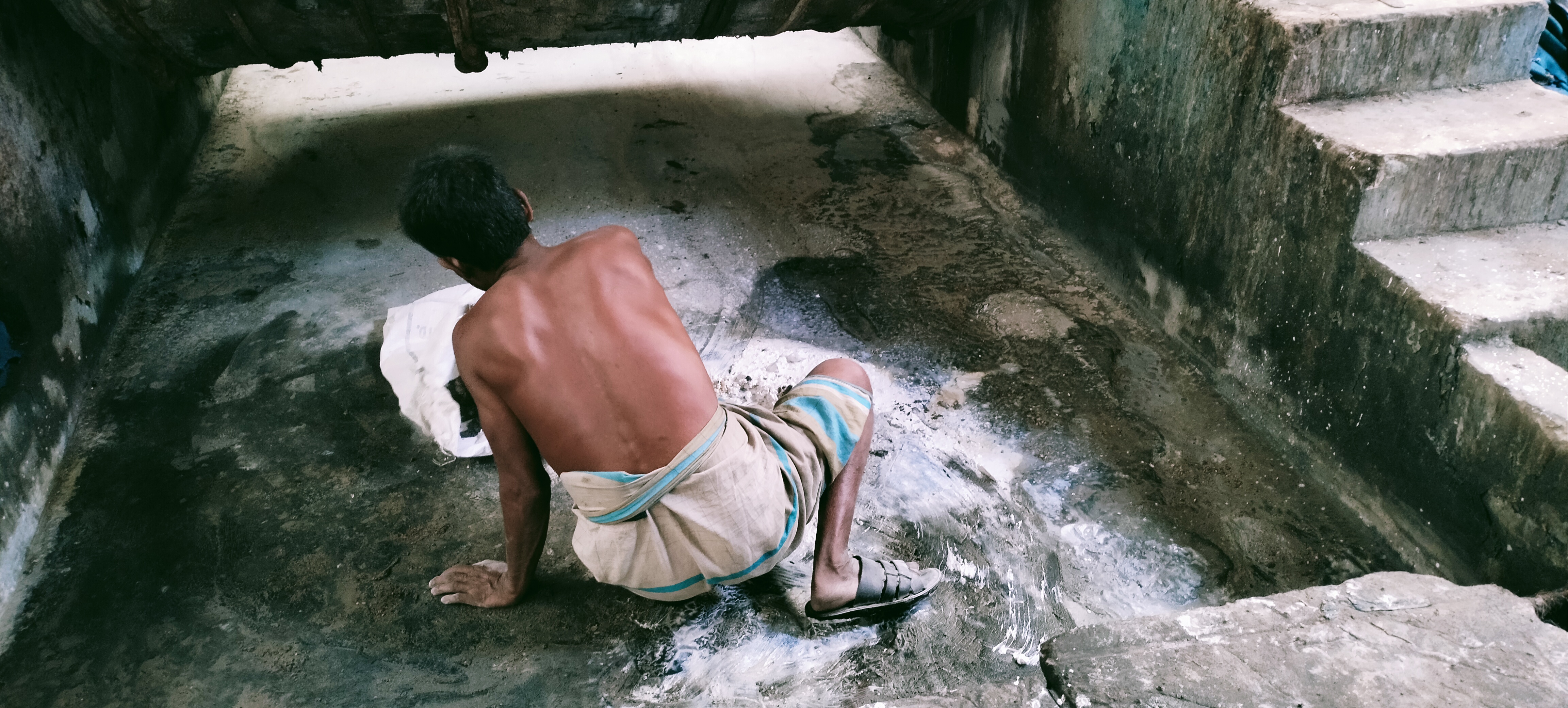
The structural design of Jahangir’s tannery is similar to most other tanning factories in Hemayetpur in that it is designed so that sufficient natural light and air can pass through the premises. The recent construction of a neighbouring factory however now prevents natural light and air from coming into Jahangir’s tannery. Whilst there are a few electric lights, the lighting is still insufficient to illuminate the entire tannery.
Conclusion
Jahangir runs a long-established and well-respected business. He demonstrates a high tolerance for risk and accepts that he will face unavoidable losses as he navigates fluctuating prices in raw materials, clients who cannot pay bills, electricity outages and staff sickness. He compensates by keeping the tannery open 24 hours a day, working long hours, paying production-based wages and hiring cheap labour, including children.
From on outsider’s perspective, the economics of Jahangir’s business and the wider supply chain system prevent the possibility of providing employees with decent and safe work. To run the business in a way that limits expenditure, Jahangir is unable to invest in safety equipment, a trained chemist or a skilled business manager. From within the supply chain system, multiple people express how the pressures on small business owners are increasing, as the sector declines. Power is concentrated among investors who prioritise profit making over a flourishing wider sector and there is less money circulating overall through the supply chain system, resulting in lower quality jobs and work environments.
An entry level job only enables a 16-year-old like Shajib to earn enough to pay for his board and food to enable him to keep working but not to save for the future, have any disposable income or support his family. He works in extremely difficult conditions and is exposed to the sun and very high temperatures all day. Raja, aged 13, also undertakes dangerous work for very little money. While neither undertake the more technical jobs in the business they are nonetheless exposed to chemicals and leather shavings, which are linked to health issues including cancer. Jobs requiring more experience involve direct contact with toxic chemicals but earn (mostly men with families) between BDT 14,000-17,000 US$130-360 a month.
Despite the forced location to Hemayetpur from Hazaribagh in 2017 – which cost Jahangir a 25% share of his business – the tannery is still operating without the infrastructure support it requires. A lack of a consistent electricity supply leads to lowered productivity and profits, and increased work hours. The lack of capacity in the Central Effluent Treatment Plant is increasing the toxicity of the work environment, surrounding neighbourhoods and food that workers and their families are eating. It is Jahangir’s observation that health issues are on the rise.